The static fuselage is gaining yet more skin sections courtesy of Laurent, and David has continued to furnish the cockpit area with items such as sidewall panels and the support structure for the fuse boxes. Lawrence has continued his work on the tail assembly and this is starting to take shape quite nicely.

Lawrence and Paul traveled west to Marazion Primary School, nestled in the shadow of St Michael’s Mount to give a presentation to Year 6 pupils whose summer topic is ‘Bright Futures Start Here’. The presentation included informing the pupils about what apprenticeships can offer them, an overview of our projects, an insight into daily life in a workshop and information about what grades and qualifications are required for our given trades.
Paul was even asked to give a talk about life in the RAF which took him back to his old recruitment office days! In exchange, the pupils fired some very well thought out and pressing questions at us and hopefully some came away with a better idea of what they would like to do in the future.
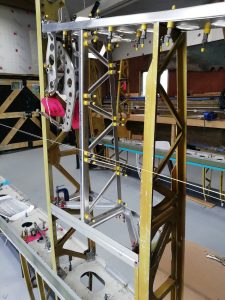
Progress on the wings has seen some aileron control structure fitted to the aft spar, along with the auxiliary spar and centre rib 15. Once those parts for the starboard wing were fabricated and fitted, the mirroring parts for the port wing were fabricated and stored ready for later fitment. In the main workshop, Murphy has been continuing his fabrication on nose rib 10 for the port wing. Once finished he will then be starting fabrication of the same rib for the starboard wing. While now in the wing-shed, focus has now shifted back towards the root of the wing and in particular the wheel well area. While awaiting some more information to help correctly fabricate centre rib 8, I have focused my attention into fabricating the auxiliary spar that joins rib 5 and 8 together aft of the main undercarriage bay.
While it may appear relatively simple at first on the 2D drawing, you soon realise that not only is it mounted on an angle within the wing, it has various folds at differing angles, and comprised of 4 individual components. The angles for example are shaped in 3 different planes, causing the material to be bent into ways that it doesn’t want to go. Using everyone’s knowledge from across the team and Laurent in particular has ensured that we have now been able to fabricate the bulk of the whole item, with only the simpler components remaining before moving onto the next stage. All Images © Parnall Aircraft Company Ltd